A crucial piece of equipment in many manufacturing processes, particularly in the manufacturing of pharmaceuticals, is the press equipment in the industry.
작성자 정보
- Brandon 작성
- 작성일
본문
Due to constant operation and use, wear and tear on the filter machine is inevitable, resulting in a decline in its effectiveness.
Proper servicing including replacement of various parts and the entire press is essential to extend its lifespan and avert costly breakdowns.
Filter Replacement Cycle
The process for oil filter manufacturer in india replacement depends on application and type of the machine. Generally, the cycle involves regular replacement of filter cloths and cake filter plates.
On average, these components have a shelf life of 4-8 years, dependent on the operating conditions and make of the press.
The whole press equipment alone needs renewal after 10-20 years of continuous running.
However, in some examples, the replacement can be more frequent due to excessive wear and tear or modifications in operating conditions.
Filter Replacement Procedure
Replacing a filter involves the following steps:
1 Pre-planning: Before initiating the renewal process, conduct a complete inspection of the filter and identify the components that require renewal. Create a detailed checklist of the necessary components, tools, and materials.
2 Disabling the filter: Separate the electricity and isolate the filter from the manufacturing process.
3 Removing the press media: Start by removing the press cloths from the diaphragm plates.
4 Replacing the follower plates: Take out the support plates and renew them with recent ones. Ensure proper positioning of the plates during the renewal process.
5 Renewing the diaphragm plates: Take out the used filter surfaces and replace them with new ones. Ensure they fit properly and are securely fastened.
6 Renewing the whole filter: If necessary, renew the whole press with a new one. This involves removing all the parts and coupling surfaces, as well as attaching them to the new equipment.
7 Wiping and maintenance: Once the replacement is finished, completely clean and inspect the new parts and the press.
In summary, the renewal process and procedure of a filter is an critical part of preserving its efficiency and performance in various industrial operations.
By following the processes outlined above, plant operators and servicing personnel can ensure the shelf life of the equipment and avert costly breakdowns.
Regular maintenance and evaluations can assist to increase the shelf life of the press and give to a smooth production process.
Proper servicing including replacement of various parts and the entire press is essential to extend its lifespan and avert costly breakdowns.
Filter Replacement Cycle
The process for oil filter manufacturer in india replacement depends on application and type of the machine. Generally, the cycle involves regular replacement of filter cloths and cake filter plates.
On average, these components have a shelf life of 4-8 years, dependent on the operating conditions and make of the press.
The whole press equipment alone needs renewal after 10-20 years of continuous running.
However, in some examples, the replacement can be more frequent due to excessive wear and tear or modifications in operating conditions.
Filter Replacement Procedure
Replacing a filter involves the following steps:
1 Pre-planning: Before initiating the renewal process, conduct a complete inspection of the filter and identify the components that require renewal. Create a detailed checklist of the necessary components, tools, and materials.
2 Disabling the filter: Separate the electricity and isolate the filter from the manufacturing process.
3 Removing the press media: Start by removing the press cloths from the diaphragm plates.
4 Replacing the follower plates: Take out the support plates and renew them with recent ones. Ensure proper positioning of the plates during the renewal process.
5 Renewing the diaphragm plates: Take out the used filter surfaces and replace them with new ones. Ensure they fit properly and are securely fastened.
6 Renewing the whole filter: If necessary, renew the whole press with a new one. This involves removing all the parts and coupling surfaces, as well as attaching them to the new equipment.
7 Wiping and maintenance: Once the replacement is finished, completely clean and inspect the new parts and the press.
In summary, the renewal process and procedure of a filter is an critical part of preserving its efficiency and performance in various industrial operations.
By following the processes outlined above, plant operators and servicing personnel can ensure the shelf life of the equipment and avert costly breakdowns.
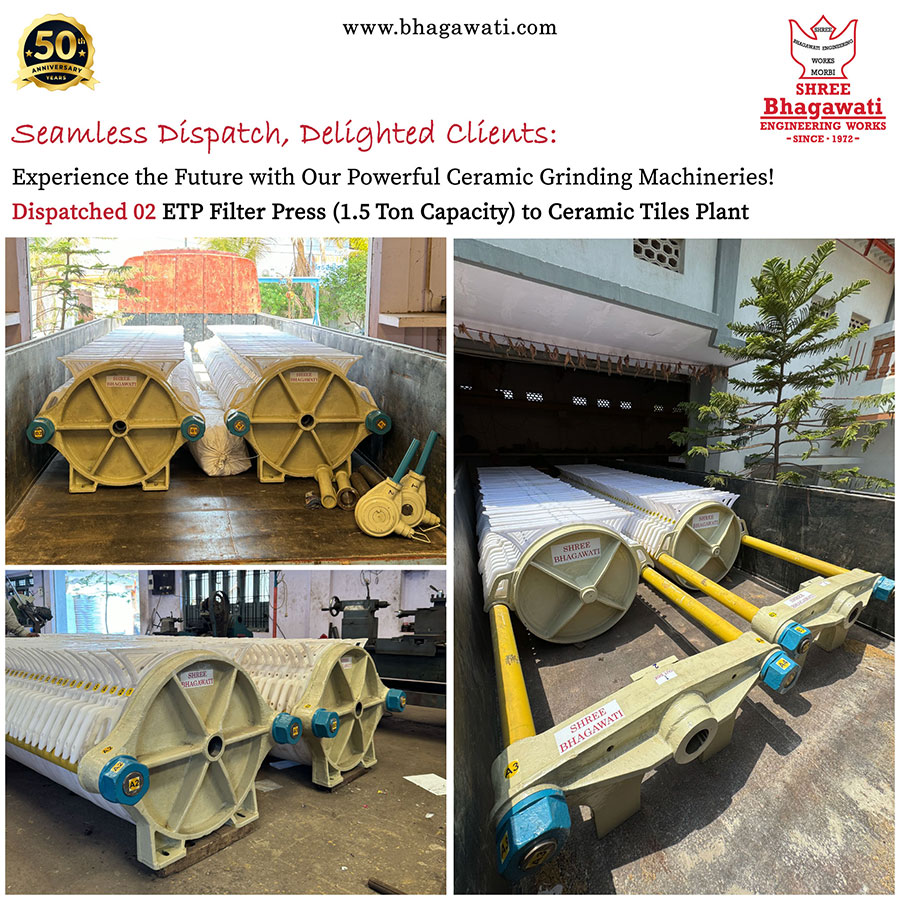
관련자료
-
이전
-
다음
댓글 0
등록된 댓글이 없습니다.